製造工程
原料工程
原料配合
目的の材質特性に合った様々な金属酸化物等を精密に計量し配合します。
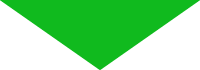
混合粉砕
●ボールミル
セラミックボールを充填したミルという装置に原材料粉末と水を入れ、装置を回転や振動させ粉砕を行います。その後バインダー等の添加剤を加え混合しスラリー(固体と液体が混ざった泥状のもの)を作ります。
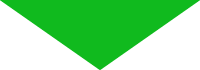
噴霧乾燥
●スプレードライヤー
出来たスラリーをこの装置で噴霧し、そこに熱風を当てて乾燥・造粒します。
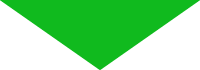
完成原料
造粒された完成原料の中には原材料、水分、バインダー等が入っていて、次の工程で製品形状の大部分を決める金型に投入され成形されます。
成形工程
成形
●成形(金型成形)
メカプレス・油圧プレス等、金型による量産成形を得意としています。また千葉セラミック独自の技術により難形状への挑戦を常に行っています。
●押出し成形
トコロテンのように、粘土状原料を口金を通じて押し出して成形する方法、長尺製品、パイプ製品、2穴製品等に適した成形方法で、各種標準サイズの製品を取り揃えております。
●CIP成形(冷間静水圧成形)(ウェット&ドライ)
ゴム型に粉体を充填して、水圧(油圧)で均等に圧力を掛ける成形方法。特殊形状製品の成形やグリーン加工の為のセラミック素材等の生産に使われます。
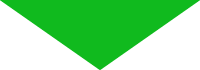
グリーン加工
プレス成形、CIP成形した焼結前のセラミック素材から、下記の様々な加工方法で製品形状に加工します。 研削加工(焼結後の加工)より、安価に設定できます。(寸法精度ご相談下さい!)
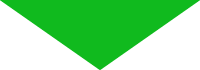
切削加工
旋盤・NCにて切削加工致します。
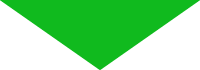
切断
切断加工・ダイシング・溝入れV溝加工、各種形状、深さに対応ピッチ精度御相談下さい。
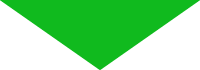
穴あけ
ネジ切り
セラミック材料への穴あけ、ネジ切り、ザグリ加工等御相談下さい。
焼成工程
焼成
連続焼成炉による量産から、パッチ式焼成炉による試作まで、1個から量産まで幅広く対応させて頂きます。
その他、還元雰囲気炉、真空焼成炉も設備しており、様々な材料に対応しております。
二次加工工程
焼結後のセラミックスを目的に合った下記の様々な方法で加工します。
平面研削
ラッピング
表面粗さがサブミクロン以下の加工が可能の上、量産にも適用可能です。
鏡面研磨
ポリシング
~φ300mm セラミックス板に、鏡面仕上げが可能です。
円筒・内外周
円筒研削・ホーニング
ポンプシャフト、真円度、はめ合い公差等、御相談下さい。
超音波加工
微細加工・穴あけ・ネジ切り
微細加工が可能に、
加工精度、御相談下さい。
レーザー加工
スクライブ・穴あけ・切断
セラミック材料への微細加工の他、様々な材質の加工も御相談下さい
メタライズ
銀電極付け、ロウ付け用メタライズ
セラミックス基盤、半導体セラミックス等の銀焼付け、協力会社等のネットワークにより、ロウ付け用メタライズも承っております。御相談下さい。
ガラスシール
独自の技術により、セラミックと金属をガラスを用いて封着・接着を行っております。各種気密端子、電子管等に利用されます。
検査工程
検査・出荷
図面通りに仕上がっているか最終確認をし、梱包・出荷します。
出荷
製品
様々な製品となって、社会に貢献致します。